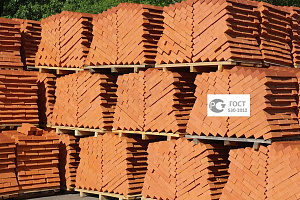
ГОСТ 530-2012 Кирпич и камень керамическиеМЕЖГОСУДАРСТВЕННЫЙ СОВЕТ ПО СТАНДАРТИЗАЦИИ, МЕТРОЛОГИИ И СЕРТИФИКАЦИИ (МГС)INTERSTATE...
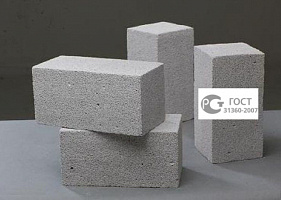
ИЗДЕЛИЯ СТЕНОВЫЕ НЕАРМИРОВАННЫЕ ИЗ ЯЧЕИСТОГО БЕТОНА АВТОКЛАВНОГО ТВЕРДЕНИЯ ГОСТ 31360-2007 ...
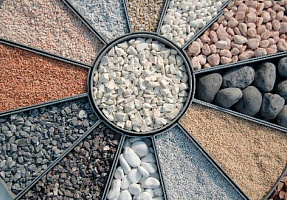
ГРАВИЙ, ЩЕБЕНЬ И ПЕСОК ИСКУССТВЕННЫЕ ПОРИСТЫЕ ГОСТ 9757–90 ГОСУДАРСТВЕННЫЙ СТАНДАРТ СОЮЗА ССР ...
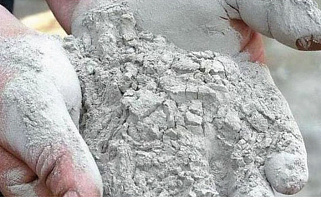
ПОРТЛАНДЦЕМЕНТ И ШЛАКОПОРТЛАНДЦЕМЕНТ ГОСТ 10178—85 ГОСУДАРСТВЕННЫЙ СТАНДАРТ СОЮЗА ССР ПОРТЛАНДЦЕМЕНТ...
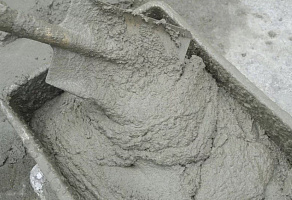
РАСТВОРЫ СТРОИТЕЛЬНЫЕ ГОСТ 28013—98 МЕЖГОСУДАРСТВЕННЫЙ СТАНДАРТ РАСТВОРЫ СТРОИТЕЛЬНЫЕ ...
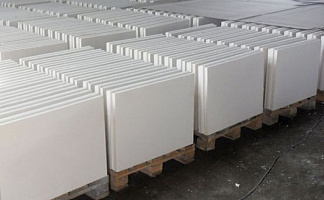
ПЛИТЫ ГИПСОВЫЕ ДЛЯ ПЕРЕГОРОДОК ГОСТ 6428-83 ГОСУДАРСТВЕННЫЙ СТАНДАРТ СОЮЗА ССР ...
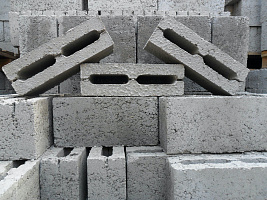
КАМНИ БЕТОННЫЕ СТЕНОВЫЕ ГОСТ 6133-99 МЕЖГОСУДАРСТВЕННЫЙ СТАНДАРТ ...
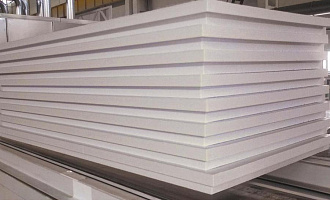
ПЛИТЫ ПЕНОПОЛИСТИРОЛЬНЫЕ ГОСТ 15588–86 ГОСУДАРСТВЕННЫЙ СТАНДАРТ СОЮЗА ССР ...
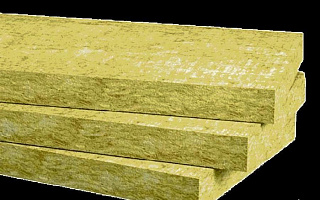
ПЛИТЫ ИЗ МИНЕРАЛЬНОЙ ВАТЫ НА СИНТЕТИЧЕСКОМ СВЯЗУЮЩЕМ ТЕПЛОИЗОЛЯЦИОННЫЕ Технические условия ГОСТ...

ИЗДЕЛИЯ ИЗ ЯЧЕИСТЫХ БЕТОНОВ ТЕПЛОИЗОЛЯЦИОННЫЕ ГОСТ 5742–76 ГОСУДАРСТВЕННЫЙ СТАНДАРТ...
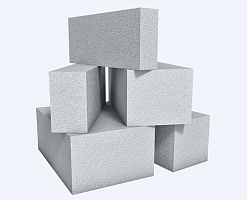
БЛОКИ ИЗ ЯЧЕИСТЫХ БЕТОНОВ СТЕНОВЫЕ МЕЛКИЕ ГОСТ 21520–89 МЕЖГОСУДАРСТВЕННЫЙ СТАНДАРТ БЛОКИ...
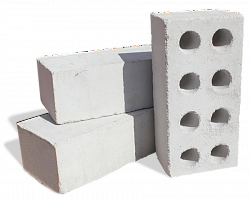
КИРПИЧ И КАМЕНЬ СИЛИКАТНЫЕ ГОСТ 379–95 МЕЖГОСУДАРСТВЕННЫЙ СТАНДАРТ КИРПИЧ И КАМЕНЬ СИЛИКАТНЫЕ Технические...
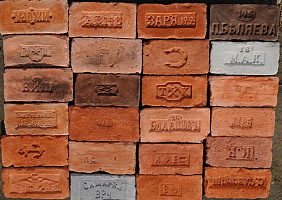
КИРПИЧ И КАМЕНЬ КЕРАМИЧЕСКИЕ ГОСТ 530-95 МЕЖГОСУДАРСТВЕННЫЙ СТАНДАРТ ...
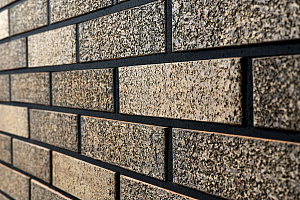
КИРПИЧ И КАМНИ КЕРАМИЧЕСКИЕ ЛИЦЕВЫЕ ГОСТ 7484-78 МЕЖГОСУДАРСТВЕННЫЙ СТАНДАРТ ...
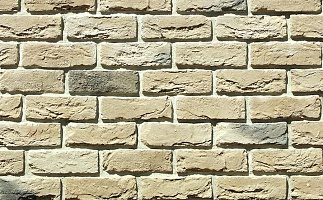
КИРПИЧ И КАМЕНЬ КЕРАМИЧЕСКИЕ ГОСТ 530–2007 МЕЖГОСУДАРСТВЕННЫЙ СТАНДАРТ ГОСТ 530–2007 КИРПИЧ И КАМЕНЬ...
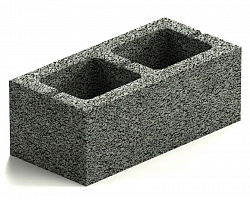
БЕТОНЫ ЯЧЕИСТЫЕ ГОСТ 25485-89 МЕЖГОСУДАРСТВЕННЫЙ СТАНДАРТ БЕТОНЫ ЯЧЕИСТЫЕ Технические...